Sous-Vide 101: Low-Temperature Chicken
J. Kenji López-Alt
There is a misconception about food safety, and particularly as it applies to low-temperature water bath cooking (often inaccurately referred to as “sous-vide” cooking*). The thought process goes something like this:
*Sous-vide refers only to the vacuum-packing aspect, which, while it often goes hand in hand with low-temp water baths, it is not the defining characteristic of the cooking technique.
Point 1: Industry-standard food safety instructions refer to the range between 40°F and 140°F as the bacterial “danger zone,” and recommend not allowing any foods to sit within that range for any longer than four hours.
Point 2: Low-temperature cooking often takes place in temperature ranges within this “danger zone.” For example, cooking a steak for several hours at 130°F.
Conclusion: Low-temperature cooking is unsafe.
It seems reasonable to make such an assumption, but it ignores one important factor: industry standards for food safety are designed to be simple to understand at the expense of accuracy. The rules are set up such that anybody from a turn-and-burner at Applebee’s to the fry-dunker at McDonald’s can grasp them, ensuring safety across the board.
But for single-celled organisms, bacteria are surprisingly complex, and despite what any ServSafe chart might have you believe, they refuse to be categorized into a step function. A number of factors, including saltiness, sweetness, moisture, and fat content can affect growth, not to mention the effects of temperature are much more subtle.
For instance, take a look at the graph below. The data was taken directly from the USDA’s guide to obtaining a 7.0 log10 relative reduction in salmonella in chicken. For those of you who don’t know what a 7.0 log10 relative reduction is, it’s the bacterial equivalent of sticking a stick of dynamite in an anthill. The vast majority of the baddies become harmless, dead, ex-baddies.
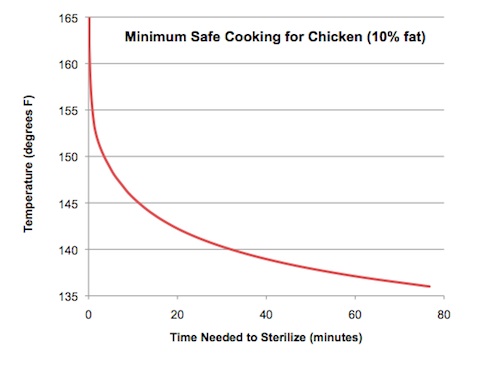
Essentially, the red line in this graph indicates how long a piece of chicken needs to be cooked at a specific temperature in order to be deemed safe for consumption. So, for example, we see that at 165°F, the chicken is safe pretty much instantaneously (hence the 165°F minimum internal temperature recommendation by the USDA—they are being very conservative and assuming you will bite into it the second it reaches that temp). Whereas at 140°F, the chicken needs to be held for 35 minutes to be safe.
Now with a conventional oven, this chart is totally useless. Since your cooking environment is much higher than your desired final temperature there is no way to hold your meat at a steady low temperature—it hits 140°F, then continues to go up and up and up. So the best you can do is take the center to 165°F to ensure that the entire piece of chicken is safe to consume, by which point it’s already expelled a great deal of its moisture.
Low-temperature cooking changes all of that. With a temperature-controlled water bath, you have the ability to not only cook chicken to lower temperatures, but more importantly, to hold it there until it’s completely safe to consume.
While the recipe that follows is easiest with a controlled water bath, feel free to use my cheap and easy cooler hack to do it ghetto-style.
Continue here for Sous-Vide Chicken with Sun-Dried Tomato Vinaigrette »
Even though a cooler is designed to keep things cool, there’s no reason why it shouldn’t perform equally well at keeping hot things hot, right? The principles are the same—the interior of the cooler is separated from the outside environment with two layers of plastic with a vacuum in between them. Heat transfer is minimized, thus any volume of hot water inside the cooler should stay hot for a long, long time. That’s pretty exciting.
The other part of precision low-temperature cooking is vacuum sealing the food. This is necessary primarily because when placed in the water bath, any air bubbles left in the bag will insulate the food within, causing uneven cooking. That said, the strong vacuum provided by a commercial chamber vac or a food saver are completely unnecessary for most cooking applications. In fact, the only thing you need to do is ensure that your cooking bag has no bubbles in it.
Thanks to a tip I gleaned a couple of weeks ago from Dave Arnold of the French Culinary Institute, achieving this is a snap. It uses the simple property of displacement. All you have to do is place your food in a regular zipper-lock bag, seal the zipper most of the way, then slowly dip it into a large volume of water, keeping the zipper-lock end above the water line.
As you submerge it, air should be steadily squeezed out (sometimes a little coaxing is necessary), and the bag will conform to the shape of its contents. Once you get the the very top, seal the bag, and there you go: food sealed in a perfectly air-free environment.
Hard pressed office worker and cook here. If I go home at lunchtime and put in a medium sized chicken to roast in the oven can I ensure it’s ready to eat when the family get in in the evening?
I’ve found a recipe instructing me to roast at 120C for 5 hours, uncovered. The recipe mentions ensuring it reaches 85C internally.
Does that sound reasonable? Any other tips to ensure I don’t risk a charred/undercooked bird?
A few days ago I printed out a recipe from peacefulnightdove “BEST Slow-Roasted Chicken”. It sounded wonderful but was to be roasted at 250 F (126 C) degrees for 5 hours. That sounded like a low temperature to me, so I emailed the County Nutritionist and Health Agent where I lived. Here is her reply: Good for you JoAnn to be suspicious! That is definitely outside the USDA guidelines, and yes bacteria may well be growing for quite a while in there. Poultry especially should not be done at less than 325 degrees. You could use the same spices and onions, increase the temp to 325 and decrease the time. Figure about 20 min per pound for the time. The safest way is to use a meat thermometer, final temp in the thigh should be 180 degrees. http://community.tasteofhome.com/forums/t/173823.aspx
Staying with old friends over the weekend, and on Sunday, my hostess – who is a great cook – asked would I mind if she did something simple for dinner, a roast chicken.
Since it’s possibly my fav dish, I agreed heartily, and she immediately got to work and switched on the oven. It was only mid-afternoon, and I asked what time she planned to have dinner at.
‘Oh the chicken will be done about 7.00, so we’ll eat shortly after that’. That meant a three-hour cooking time!
I asked her what temperature she was cooking the chicken at and she told me 300F, which I scarcely believed. ‘Well, I don’t like it all dried out, and I like it really falling off the bone, so I like to cook it slowly’.
Of course we debated the pros and cons of high versus low temperature. I was intrigued by the idea of a slow roasted chicken, how it would taste, and whether it really wouldn’t be dried out.
Here’s what she did:
4lb chicken
sprinkled liberally with sea salt, and herbes de provence
No trussing, and nothing in the cavity
Covered generously with thick-cut canadian bacon on the breast
Before putting it in the oven, she put a foil tent over the breast, which she removed about half an hour before taking the chicken out.
The result was one of the most delicious, moist, and tender roast chickens I have ever eaten. It made me think a lot about the 450F oven I use for mine (which is really closer to a true 430F).
Roast Sticky Chicken-Rotisserie Style
Ingredients
4 teaspoons salt
2 teaspoons paprika
1 teaspoon onion powder
1 teaspoon dried thyme
1 teaspoon white pepper
1/2 teaspoon cayenne pepper
1/2 teaspoon black pepper
1/2 teaspoon garlic powder
2 onions, quartered
2 (4 pound) whole chickens
Directions
In a small bowl, mix together salt, paprika, onion powder, thyme, white pepper, black pepper, cayenne pepper, and garlic powder. Remove and discard giblets from chicken. Rinse chicken cavity, and pat dry with paper towel. Rub each chicken inside and out with spice mixture. Place 1 onion into the cavity of each chicken. Place chickens in a resealable bag or double wrap with plastic wrap. Refrigerate overnight, or at least 4 to 6 hours.
Preheat oven to 250 degrees F (120 degrees C).
Place chickens in a roasting pan. Bake uncovered for 5 hours, to a minimum internal temperature of 180 degrees F (85 degrees C). Let the chickens stand for 10 minutes before carving.
Uncle Ben got it right a few decades ago when he put his rice in little plastic bags and said to boil them up just like that.
The results were, for many American home cooks, just dandy, with fluffy rice every time. No hassle of measuring or cleaning up a dirty pan.
Then along comes something called “sous vide” — literally translated as “under vacuum” — a few decades later. This means food is cooked in Cryovac plastic containers from which the air has been completely removed. Then the bag is placed in a water bath and cooked at a low temperature for a long time.
Simmering just below the surface of this technique, however, is the question of bacterial growth from cooking and reheating at lower temperatures than recommended by some state and federal authorities.
Still, there are chefs and experts who believe the system is safe and results in more sumptuous, tender and nutritious meals.
David Ritter, 50, of Westfield — a chef instructor at The Art Institute of New York City — wholeheartedly believes in the technique and its safety.
I tend to get caught up on certain cook book authors, and for the past month it has been all about Heston Blumenthal. Head chef at the Fat Duck in the U.K., his cookbook In Search of Perfection has been fostering idea after crazy idea. In a Serious Eats article, we wrote about cooking a pizza on the bottom of a cast iron skillet, to great success. The best part is that his mad-cap search for perfection is, except for a few mentions of blowtorches, essentially plausible at home. That’s when I came to the roast chicken section.
A raw chicken is about 80 per cent water. Cooking it is basically a battle to hang on to some of that moisture, so that you end up with a deliciously succulent bird. In this recipe, two techniques help achieve that aim: brining and low-temperature cooking.
Brining is something I’ve tried before and completely recommend. But how low is the low-temperature cooking? I’d just done that a few months ago at 250 degrees. But apparently that wasn’t even close to what Heston wanted. The bird is done at 140, so he said to set the temperature there and cook it for a long time. Here’s the idea: the bird is supposed to be done cooking when it reaches 140. So put it in environment at that temperature, and wait until it gets there.
It might sound all well and good, but that’s a good 60 degrees below where my oven can go. I thought I was going to have to forget it until I came across the one instrument that I’d never considered before. The crock-pot. Here was something specifically designed to cook foods for a long time at a low temperature. Would it work?
The “hot” setting was way too hot, and even “low” maintained a temperature far above what I needed. So then I had to turn to the “keep warm” setting–you know, the one your turn to after the food is done. And like some destined fate, when I tested the temperature of the setting it came out exactly to 140. It was time to start.
Problems started immediately thereafter. Heston likes to plunge his bird in boiling water for 30 seconds to help get a crisper skin, the same method that helps those ducks in Chinatown windows look so crackly. But I haven’t a pot near that big. My biggest one would quickly lose it’s boil if I stuck a three and half pound bird in. I also didn’t brine the bird. It’s a hassle, and I wanted to see what this method would be like with just the slow cooking.
The biggest problem, however, was how Heston wanted to cook the skin. After the bird had cooked for 5 hours, the skin looks pale and gross, and needs some really high heat to make it look appetizing, not to mention crackly and tasty, the whole point of roast chicken. He advised letting it sit for an hour, and then sauteing the whole thing in a very hot pan to crisp the skin. Unfortunately, sauteing a whole bird is about as easy as it sounds, and no where near comprehensive. Blotches of burned skin appear next to untouched flesh. I don’t doubt that it can be done, but it’s really hard and not worth it. The pan was so hot the oil splattered violently when the chicken went in. I had to use a pan top as a shield to protect my own skin. It could not have gone worse.
But the meat? Absolute perfection. It was without a doubt the best chicken flavor I’d ever achieved. It was juicy, full flavored, and weirdly rich. After 5 hours in the crock pot I expected there to be all these juices floating in the bottom, but there was maybe a tablespoon–they all stay in the bird. He says that you can’t even make a sauce out of the drippings because there won’t be enough. He thinks it’s better to have a chicken full of those juices. I happen to agree with him.